Endlos-Laserschneiden vom Coil mit DIMECO und Alma – eine Partnerschaft, die rund läuft!
Veröffentlicht auf 09/06/2021
DIMECO ist der Spezialist für Anlagen für die Produktion ab Coil. Bereits seit seiner Gründung weiß das Familienunternehmen mit Sitz bei Besançon seine erstklassige technische Erfahrung mit einer starken internationalen Entwicklung zu verbinden. Vor acht Jahren brachte DIMECO eine innovative Anlage für das Endlos-Laserschneiden ab Coil auf den Markt. Diese über die Software von Alma gesteuerte Lösung wurde von Industrieunternehmen sämtlicher Branchen (Elektroausstattung, Bauwesen, Metallmöbel, Automobilteile usw.) übernommen. Das optimierte Schachteln über große Längen, die Produktivität der Software und deren Anpassung an die spezifischen Bedürfnisse jedes einzelnen Kunden bilden die Grundlage dieser erfolgreichen Partnerschaft.
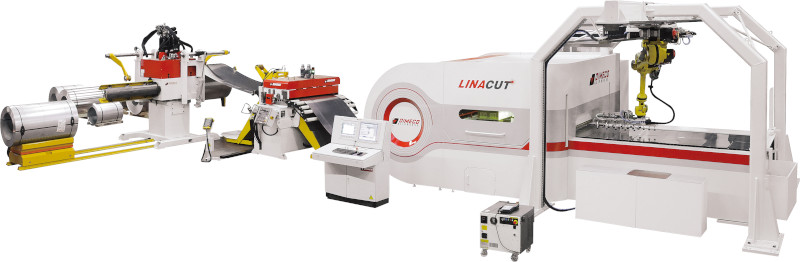
Bahnbrechende Technologie
Im Jahr 2013 präsentierte DIMECO auf der Messe Tolexpo als weltweite Vorpremiere LINACUT®, seine Linie für das Endlos-Laserschneiden ab Coil. Dank dieses innovativen Verfahrens konnte der Hersteller die Flexibilität des Laserschneidens mit der Produktivität der Arbeit mit Coils verbinden. Konkret besteht die Anlage aus einer Linie zum Abrollen der Coils, einem Modul für das Endlos-Laserschneiden und einem Modul für die Entnahme der Teile und die Entsorgung der Abfälle. Diese Anlage kann mit bis zu 25 Tonnen schweren und bis zu 2000 mm breiten Coils bestückt werden. Auch wenn die zugeschnittenen Bleche in den meisten Fällen eine Stärke zwischen 2 und 2,5 mm haben, ist die Maschine in der Lage, bis zu 4 mm starke Bleche zu bearbeiten.
„Die Technologie des Endlos-Laserschneidens ermöglicht die Produktion zahlreicher Teile unterschiedlicher Formen und Größen in großen Mengen und vollständig automatisiert mit einer äußerst niedrigen Abfallmenge“, erklärt Thibault Nosbonne, Wirtschaftsingenieur bei DIMECO. Dies ist eine große Verbesserung im Vergleich zum Stanzen/Nibbeln mit seinen Einschränkungen beim Werkzeugmanagement, auch wenn DIMECO ebenso Mischlinien für das Endlos-Schneiden fertigt, die das Laserschneiden und das Stanzen kombinieren. So lassen sich beispielsweise komplexe Formteile mit Stanzprofilen herstellen. „Ein anderer Vorteil dieses Endlos-Verfahrens im Vergleich zum Laserschneiden von Einzelblechen besteht darin, dass sehr lange Teile geschnitten werden können, die die Kapazitäten der Standard-Lasermaschinen übersteigen“, ergänzt Thibault Nosbonne. Darüber hinaus ermöglicht das Arbeiten mit Coils den Unternehmen, die ihre Teile selbst fertigen (und die Hauptnutzer der LINACUT®-Anlage sind), durch Gruppierung der Blechdicken und Coilbreiten die Rationalisierung der Produktion und die Reduzierung der Rohstoffbeschaffungskosten.
In einem automatisierten Produktionsprozess ist das automatische Entladen von Teilen und Resten ein zentrales Thema. Ein 10 Tonnen schweres, 1500 mm breites und 1 mm starkes Coil entspricht mehr als 270 Einzelblechen mit einer Länge von 3 Metern. Natürlich dauert der Coilwechsel länger als das Einlegen eines neuen Einzelblechs, aber dafür muss es nur einmal gemacht werden: Zusammen mit automatisierten Entladesystemen erhalten Sie unschlagbare Autonomie. Förderbänder, Roboter, Hebe- und Palettierungsanlagen… DIMECO bietet mehrere mit der Maschine kombinierte Anlagen, um die Teile zu entnehmen, zu sortieren und zu stapeln, wobei jede Anwendung an die spezifischen Bedürfnisse des Kunden angepasst wird.
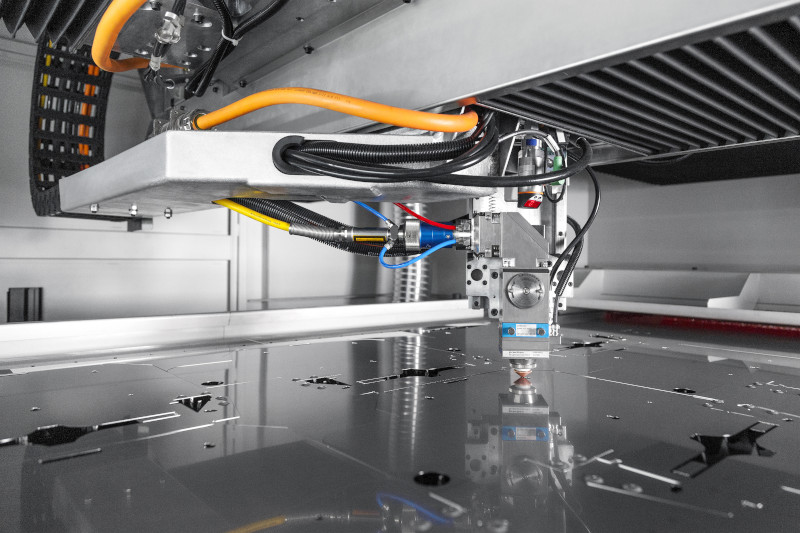
Die Schachtelsoftware – ein Teil der LINACUT®-Lösung
Für volle Leistungsfähigkeit erfordert das Endlos-Schneiden über lange Strecken den Einsatz einer hiefür geeigneten Schachtelsoftware. Daher hat DIMECO sich von Beginn an dazu entschieden, seine LINACUT®-Maschinen sowohl in Frankreich als auch weltweit mit der Software von Alma zu vermarkten. Man ist der Meinung, dass dies dank der intuitiven und automatisierten Funktionen sowohl für das automatische Schachteln der Teile jeglicher Form als auch für die Reduzierung der Programmierzeit die effizienteste Lösung ist.
Die Anpassung der Schachtelalgorithmen von Alma an die Besonderheiten der LINACUT®-Maschinen war Gegenstand umfangreicher Arbeiten. „Die Software passt sich perfekt an den Funktionsmodus unserer Maschinen an und ermöglicht ausgezeichnete Materialerträge“, bestätigt Thibault Nosbonne. „Eine vorherige Einstellung mit dem Nutzer ist jedoch immer erforderlich, um unter Berücksichtigung der jeweiligen Produktion die beste Schneidstrategie festzulegen.“
Ein weiterer Grund für die Entscheidung für die Alma-Lösung: Die Fähigkeit des Anbieters, in enger Zusammenarbeit mit dem Hersteller spezifische Lösungen für den Kunden zu entwickeln. Neben dem maschinenspezifischen Postprozessor ist dies besonders hilfreich für die Verwaltung der verschiedenen von DIMECO in die Linie für das Endlos-Schneiden integrierten Anlagen für das Entladen der Teile. Konkret übermittelt die Alma-Software an die Hebeanlage die genaue Position jedes einzelnen Teils und die Ablagestelle des Teils, doch da jeder Kunde seine Besonderheiten hat, ist die Steuerung der Palettierung stets Gegenstand individueller Anpassungen.
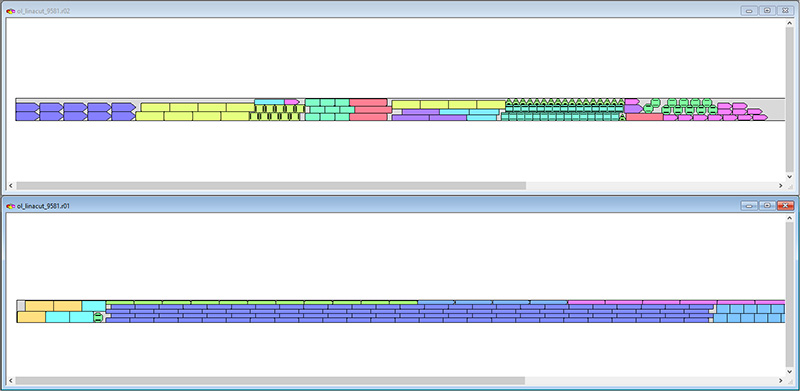
Enge Zusammenarbeit zwischen Hersteller und Anbieter
In diesem Kontext führt Alma immer eine Schulung für die Endnutzer der Software durch. Nach der Installation der Software ist darüber hinaus ein Ingenieur von DIMECO, der sich bestens mit der Software auskennt, praktisch eigens für die Unterstützung der LINACUT®-Kunden zuständig.
Sowohl bei der Ersteinstellung der Lösung als auch für die Ermittlung der Bedürfnisse der einzelnen Kunden ist die Zusammenarbeit zwischen dem Softwareanbieter und dem Hersteller unabdingbar. „Unsere Partnerschaft mit Alma ist ausgereift“, stellt Thibault Nosbonne fest. „Wir arbeiten sehr effizient mit den Anwendungsingenieuren von Alma, die die Herausforderungen der LINACUT®-Lösung verstanden haben, zusammen.“
Im Übrigen werden bereits neue Weiterentwicklungen der Software getestet, insbesondere um zum Beispiel nach einem Stromausfall an der Maschine mit dem Schneiden mitten in einer Schachtelung direkt an der richtigen Stelle fortfahren zu können. Eine stetige Suche nach Produktivitätssteigerungen, die durch eine enge Partnerschaft und eine gemeinsame, langfristige Vision möglich geworden sind.